Production Winder Upgrade
Nickel Mine
Leinster, WA
Leinster production winder is the primary source of ore from the mine to the processing plant. The winder was integrated into the underground and surface material handling systems. It was essential through the upgrade process this integration was maintained.
Key criteria - Safe, lowest cost option
Winder - Double Drum, 2x 17t skips, mine depth 1,100m
Scope of upgrade - Winder DC drive, Brake System, Control System, Safety System
How - Retrofit into existing converter room after removal of old systems. This approach reduced space requirements for the equipment. The upgrades safety system was implemented initially and operated in parallel with the existing safety protection to prove correct operation prior to starting the upgrade. This reduced project execution risk for the customer.
Learn more about the Project Scope here.
Winder area before upgrade
Converter room partially dismantled
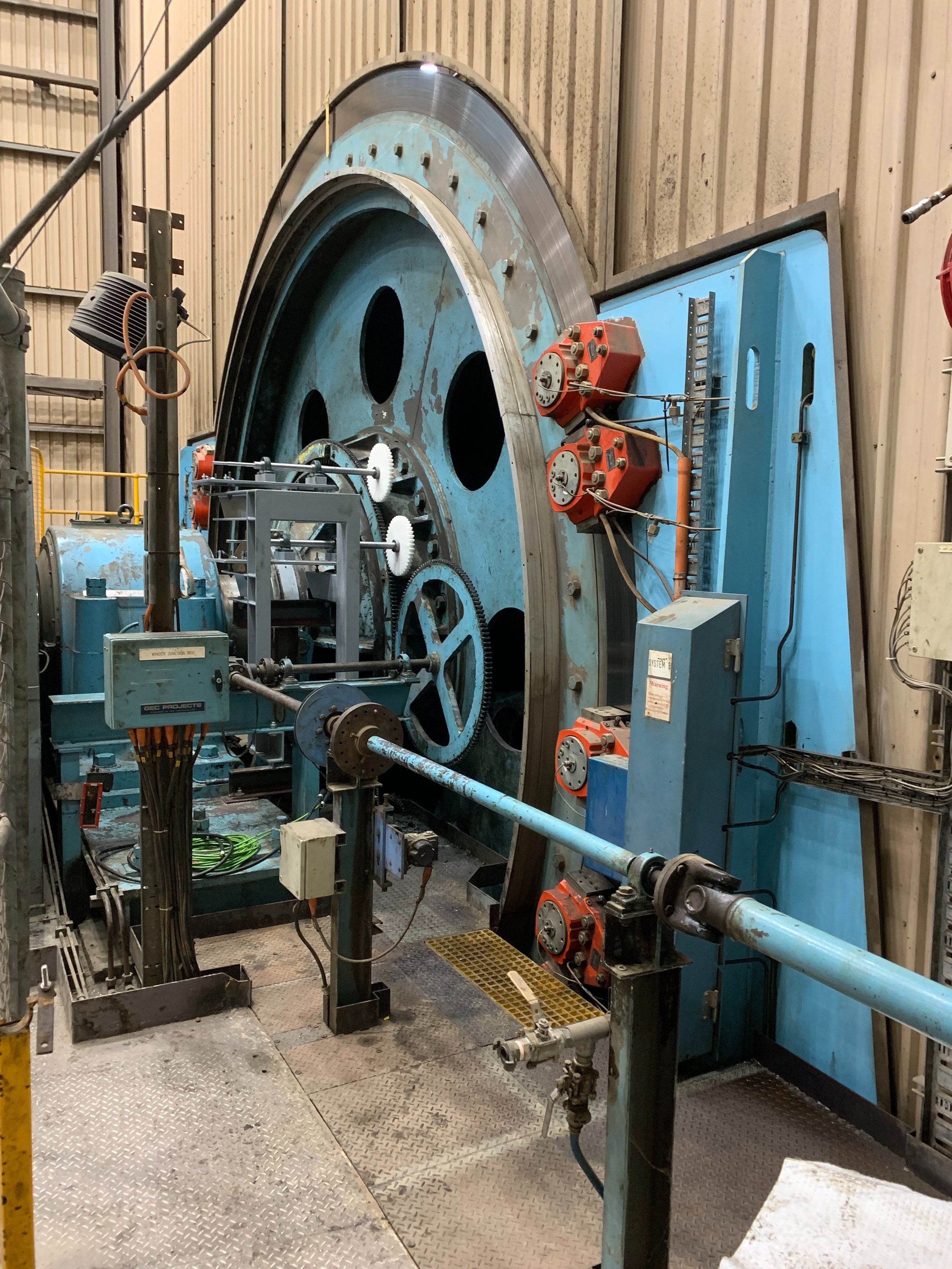
Safety system integration
Converter room partially installed
Winder drum area after upgrade
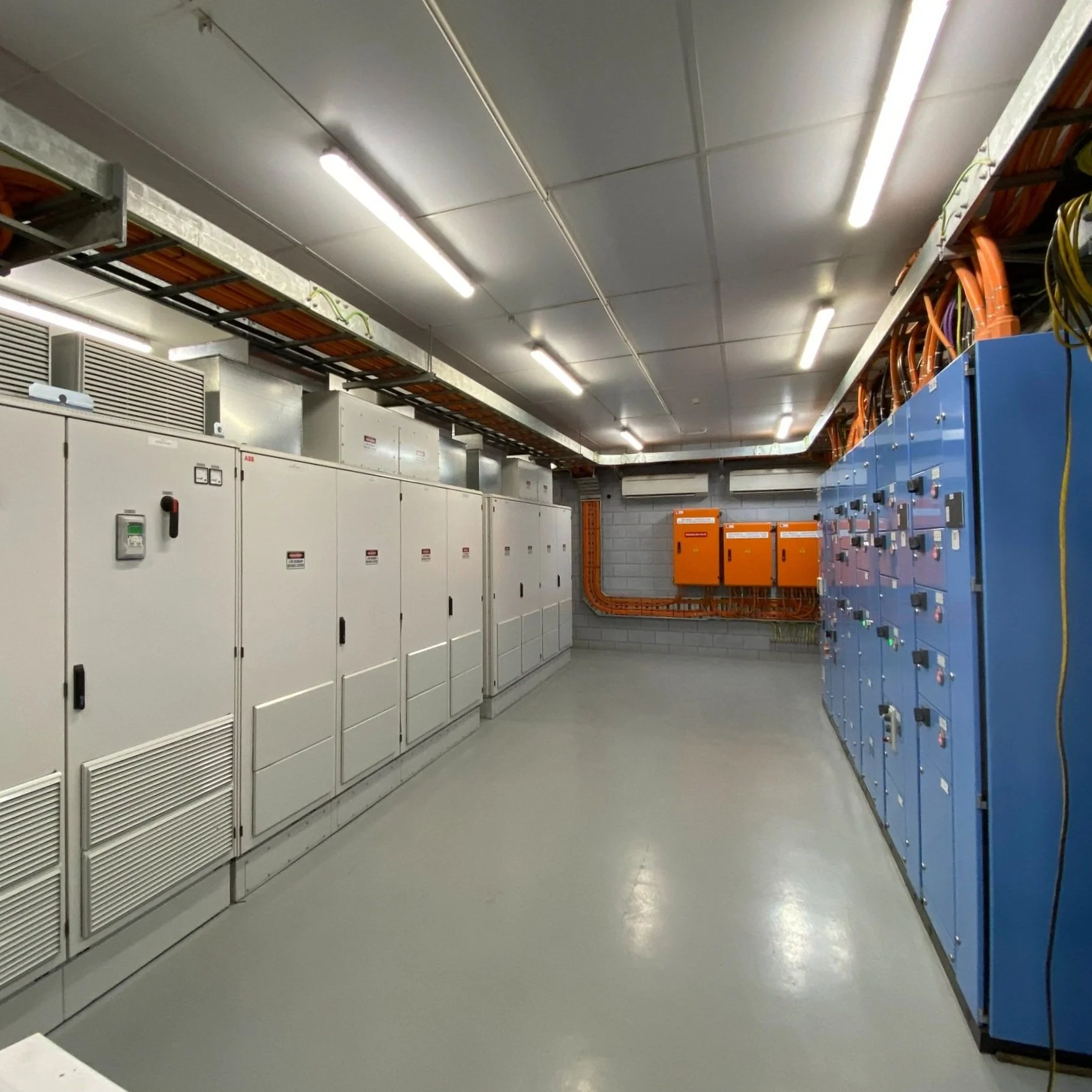
Converter room upgrade
Project Scope
-
Manage and coordinate Winder System vendor design and delivery
Coordinate Safety System specialist design and audit work
Manage and coordinate all site installation work
Coordination of all project work with site operations to minimise project impact
Manage and coordinate all logistics for project equipment and personnel
Manage all documentation and review activities
Complete upgrade was audited and verified to AS61508 compliance
Project delivered safely with no injuries
-
New Safety System
Complete Brake System & calliper replacement
Control System replacement
Conveyance communication system replacement & battery charging system
HV switchboard replacement
LV MCC replacement
ELV control supply replacement
Communication network modifications for the new systems
New drivers desk installation
To learn more about how we can work together, get in touch with us today.